Gas Mixtures in Automated Pipe Welding: When to Use Which Mixtures
- George Ficken
- Nov 19, 2023
- 2 min read
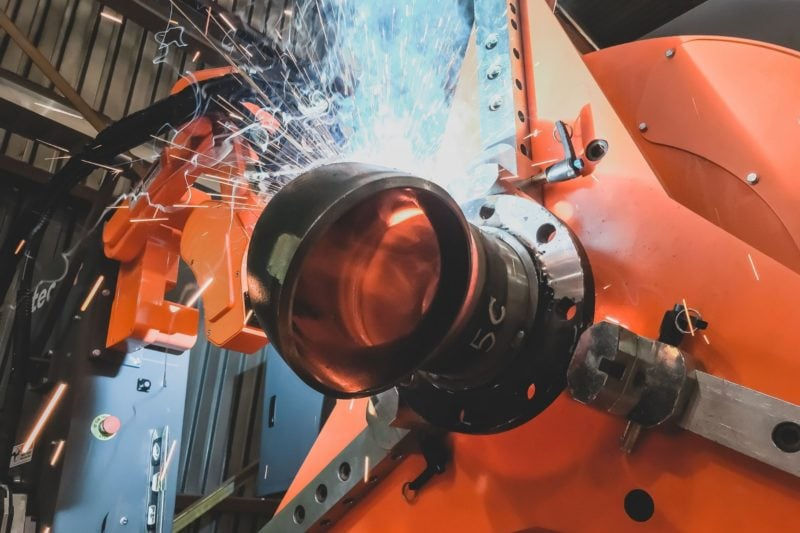
Automated pipe welding is a crucial aspect of modern industrial processes, ensuring the efficiency and precision of joining pipes for various applications. The choice of gas mixtures plays a vital role in achieving optimal weld quality, particularly when welding different pipe materials.
Carbon Steel Pipes:
For carbon steel pipes, a common gas mixture is a combination of argon and carbon dioxide. This blend provides good arc stability, deep penetration, and smooth weld beads. The carbon dioxide enhances the welding speed and helps in preventing oxidation during the process.
Stainless Steel Pipes:
Stainless steel requires a different approach. Gas mixtures containing higher levels of argon (up to 98%) are often used to shield the welding area effectively. This minimizes the risk of contamination and ensures a clean, corrosion-resistant weld.
Aluminum Pipes:
Aluminum, being highly reactive, demands a precise gas mixture. Typically, a combination of argon and helium is preferred. Helium's higher thermal conductivity helps manage the heat input effectively, preventing overheating while maintaining proper penetration.
Titanium Pipes:
Titanium welding demands a purer environment. Argon is the primary gas used, as it prevents contamination and provides the necessary shielding. The purity of the argon gas is crucial to achieving high-quality titanium welds.
Nickel Alloys:
Nickel alloys, often used in high-temperature applications, require a controlled atmosphere during welding. Argon and helium mixtures with controlled levels of oxygen are commonly employed to ensure a stable arc and prevent oxidation.
Duplex Stainless Steel:
Duplex stainless steel combines characteristics of both austenitic and ferritic stainless steels. A gas mixture with a higher proportion of argon, along with nitrogen additions, is often used for duplex welding to maintain the desired microstructure and corrosion resistance.
Copper-Nickel Alloys:
Commonly used in marine applications, copper-nickel alloys benefit from a gas mixture of argon and helium. This combination provides the necessary protection against atmospheric contamination while facilitating good fusion and weld quality.
Inconel and Other High-Temperature Alloys:
High-temperature alloys like Inconel require specialized gas mixtures to withstand extreme conditions. Argon, along with small percentages of hydrogen, is often utilized to enhance heat input control and prevent the formation of undesirable oxides.
In conclusion, the selection of gas mixtures for automated pipe welding is a critical factor influencing the quality and properties of the weld. Tailoring the gas composition to the specific characteristics of the pipe material is essential to achieve optimal results in terms of strength, corrosion resistance, and overall performance.
GSI Machinery sells and supports the Rotoweld 3.0 automated pipe welding system in the Gulf region. Reach out today for more info.