How To Properly Purge Tubes for Orbital Welding
- George Ficken
- Oct 31, 2023
- 2 min read
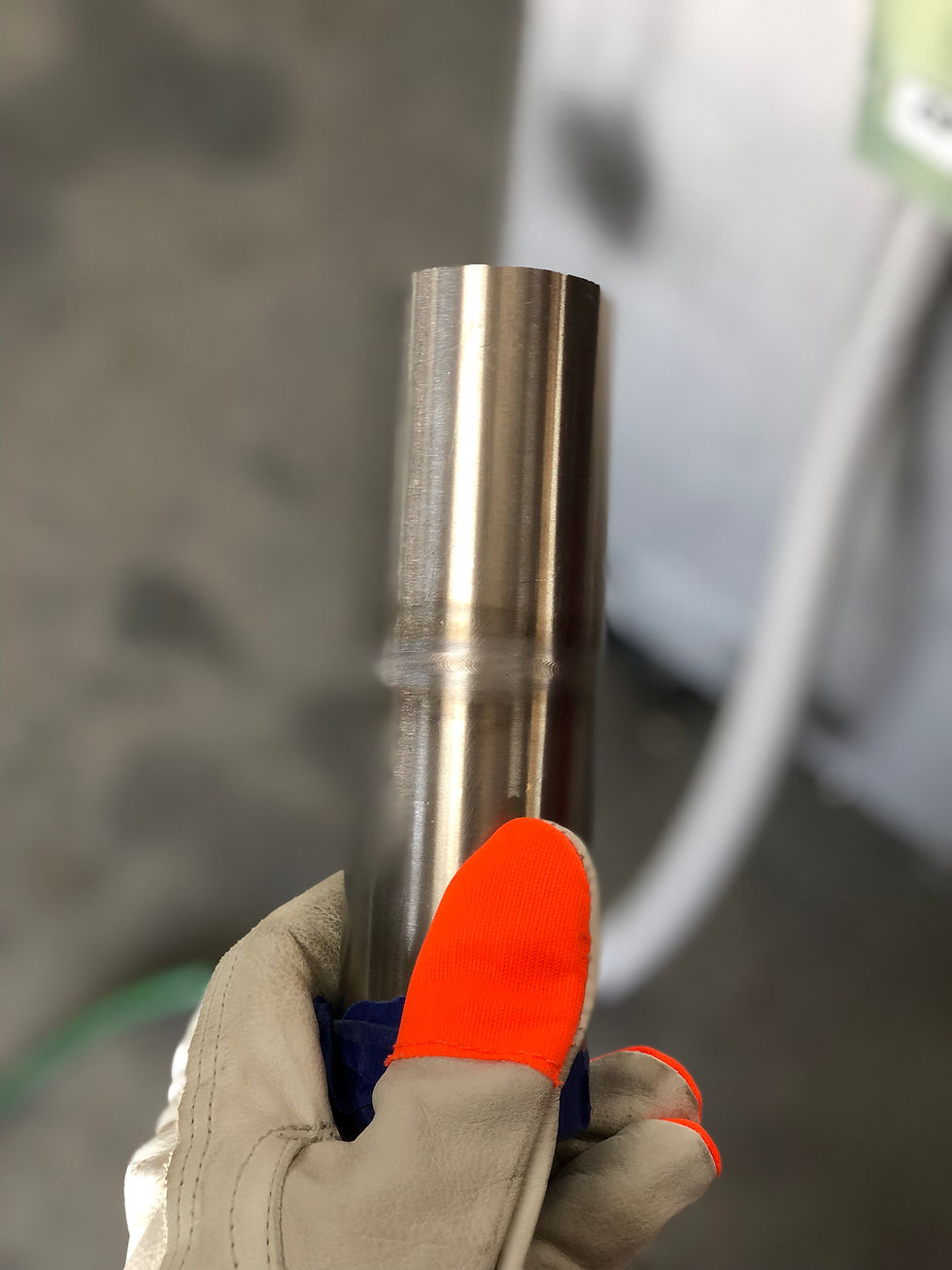
Purging a tube before welding with a closed-head orbital welding system is a crucial step to ensure the integrity and quality of the weld. Proper purging involves the removal of contaminants and oxygen from the internal space of the tube to prevent oxidation, which can compromise the weld's strength and quality. Here's a four-paragraph essay on how to properly purge a tube in preparation for closed-head orbital welding:
**1. Tube Preparation:**
Before initiating the purging process, it's essential to prepare the tube. First, ensure that the tube's ends are properly cleaned and beveled for welding. Any dirt, oil, or other contaminants on the tube's inner and outer surfaces should be thoroughly removed. Next, select the appropriate purging equipment, which typically includes a gas supply, purging device (often a gas diffuser or inflatable bladder), and pressure monitoring instruments. Position the purging equipment at one end of the tube, ensuring a secure seal between the device and the tube's inner surface.
**2. Gas Selection:**
Choose the appropriate inert gas for purging, typically argon or helium. Inert gases are used because they do not react with the metals in the tube and effectively displace the oxygen, preventing oxidation during the welding process. The choice of gas depends on factors such as the material being welded and the welding parameters. Inert gases are introduced into the tube at a flow rate sufficient to displace the air inside. It's crucial to maintain a continuous flow of the chosen gas throughout the purging process.
**3. Purge Monitoring:**
To ensure effective purging, use pressure monitoring instruments to track the progress. The pressure should be closely monitored to ensure that the inert gas has fully displaced the oxygen and that the tube's internal environment remains at a low oxygen level. Typically, a drop in pressure indicates that the purging process is not yet complete. Continue the flow of inert gas until a stable pressure is reached, indicating a minimal presence of oxygen within the tube.
**4. Welding Process:**
Once the tube is thoroughly purged and the desired low oxygen environment is maintained, you can proceed with the closed-head orbital welding process. The absence of oxygen inside the tube ensures that the weld area is protected from oxidation, resulting in a high-quality, strong, and reliable weld. Ensure that the welding parameters, such as current, voltage, and welding speed, are appropriately set for the specific tube and material to achieve the desired weld quality.
In conclusion, proper purging of a tube before closed-head orbital welding is essential to maintain the quality and integrity of the weld. Adequate tube preparation, gas selection, continuous purging monitoring, and adherence to the welding parameters all contribute to the successful execution of this critical welding process. By following these steps, welders can ensure that the resulting weld is free from defects and maintains its structural integrity, especially in critical applications.
Reach out to GSI Machinery for everything needed to properly purge your tubing before welding. We offer everything from cutting and facing tools to purge kits and orbital welding machine rentals. Contact us today for expert support on your next orbital welding project.