How to Select an Automated Pipe Welding Machine
- George Ficken
- 15 hours ago
- 6 min read

With many different options on the market today for automating your pipe welding processes, how does one make a decision and what should be considered? In this article we are going to talk about the different automated pipe welding machines on the market today and how to make sense of the noise.
What welding processes do you want to automate?
First and foremost: what welding process(es) do you want to automate? You should think about what kind of welding you do the most of and what is you highest return to automate. Do you do a lot of carbon steel pipe welding? Do you do more or less stainless steel welding? What is your current welding process for each? If you are primarily performing GMAW welds on carbon steel that would draw us more towards a machine like the Rotoweld. If you are welding GTAW all day everyday then a GTAW specific machine like the M3 may make more sense. However, if you can alter your welding procedure to allow for a GMAW root and either GMAW or FCAW fill and cap passes, then you may look more towards the Rotoweld. Traditionally, alloys were always preferred to have at least the root pass be GTAW however, with the advancement of robotic welding more and more we are seeing robotic GMAW welds meet the penetration, uniformity and fusion standards required. If you can get away with a GMAW weld throughout this is a huge benefit not only for costs per weld and level of automation available but also for deposition rate and welding speed.
So this is the first step, you need to know what pipe welding process you do the most of and therefore what process will you see the greatest benefit from automating. Also if there is room to change current welding procedures to allow for GMAW roots, this can be a huge benefit that should be explored. Many CWI's are often surprised at the level of uniformity, penetration and fusion quality from robotic GMAW welds. If you do 90% GMAW pipe welding and 10% GTAW welding it might not make sense to invest in a dual purpose machine that is slower on GMAW just so you can get the 10% TIG welding done as well. It may be the case (based on volume) that overall, you would actually gain much more production by focusing on the GMAW automation and getting that as fast as possible.
How automated do you want this process to be?
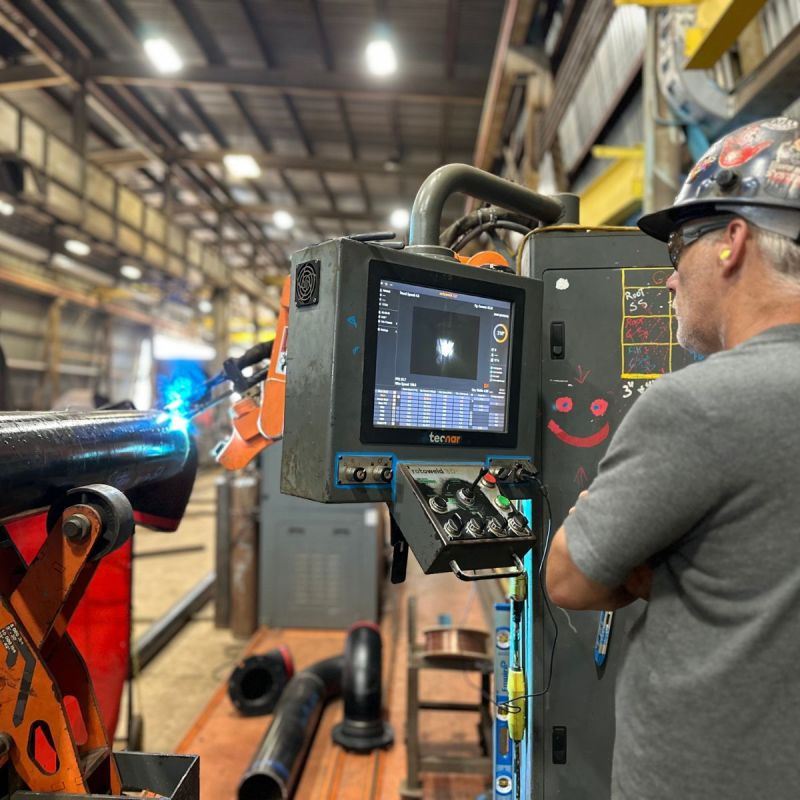
Automation is a word that gets thrown around a lot these days. When you are considering an automated pipe welding machine, you should ask yourself what do we mean by "automated" and are we really in the market for a fully automated system or are we in the market for a mechanized or semi-automated machine? When we refer to a machine as automated, like the Rotoweld, we mean the entire welding process is automated with no operator input or manipulation needed. This means that the machine will make perfect welds from root to cap with no operator manipulation. Material handling will still be somewhat manual but the welding process is automated. This automation includes bringing the torch to the pipe, selecting the torch angle and selecting the torch distance from the pipe on each weld. If you are manually setting the torch into place, squaring it, moving the torch angle and setting the torch gap from the pipe this is a manual process that is prone to error. If you are controlling the torch with a joystick to make weld adjustments on the fly to compensate for pipe misalignment, this is also a manual process that is prone to error. That is not to say that you cannot realize production gains with these methods but it is important to know the potential pitfalls of these systems and potential for production bottlenecks.
Another area of automation to consider is weld schedule generation or programming. Does the machine you are considering require manual programming and or weld schedule generation? Weld schedule generation can be a very arduous, time consuming task and will require a new program with every change in material grade, pipe size and or wall thickness. It can even change based on ambient temperatures and material quality. On the Rotoweld system for example, the machine will automatically generate a base welding program based on a pipe material, pipe OD and wall thickness in a matter of seconds. From this base program the machine uses AI to constantly measure the weld gap, bevel angle and high-low alignment to make its own welding adjustments in real time with no operator input needed. This means you can be welding within minutes of setting a completely new pipe in the chuck.
Build quality and on-going service

Lastly, it is really important to consider the build quality of the machines you are evaluating. Does the OEM make their own positioners, robotic welding arms and hardware? Are the components on the machine designed specifically for automated welding or are they bring repurposed for automated welding? Who will support the machine post-sale? How soon are you able to get replacement parts? How prone is the machine to having mechanical issues? Who makes the software of this machine is it made by the OEM or by a third party?
When considering components of the machine you really want to be sure that the OEM of the welding machine makes the components themselves. This includes the positioners, robotic arms, and even the software. Welding positioners made by positioner companies are usually intended for manual welding and thus are made with gears, commonly used are spur gears. These gears wear over time as any gear does and play begins to develop in the positioner. When manual welding this is no problem, you simply account for the play in the gears as you are welding. But in automated welding the computer cannot recognize or measure the slop that is present in the positioner and this is likely cause weld defects. For example a machine like the Rotoweld manufactures their own positioners which are electric direct drive positioners with no gears. This means the machine has smooth, high torque movement without the possibility of slop developing over time. The robotic arm is important to consider as well. Robotic arms typically seen on cobots require a lot of programming due to the high number of axis of travel they have and this creates more varaibles to control with the programming or automated software. Companies like Rotoweld build their own robotic arms from scratch with only the needed number of axis of travel. This helps to simplify programming and also includes less moving parts to be serviced and or fail over time. This makes for a very simple, robust and easily programmed robotic arm. It also means that the robotic arm will be serviceable for the life of the machine since Rotoweld built it. Cobot welding arms are rapidly changing and developing and 10 years from now getting parts and service on an older model robotic arm could be challenging.
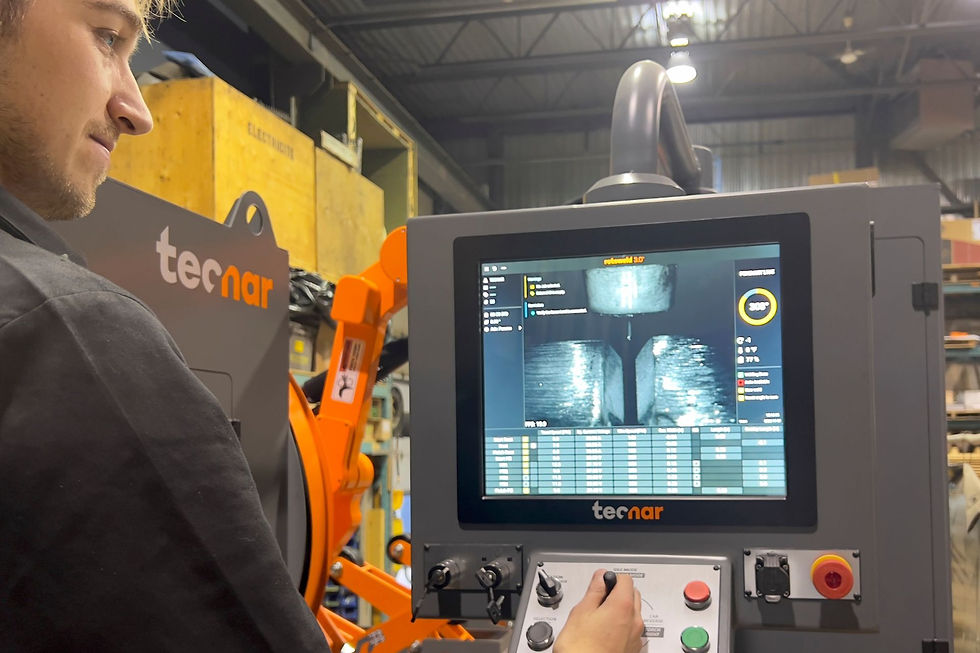
Lasty is the software. This is very important: does the OEM build their own software? If the OEM is using a third party software this can be a liability because the OEM cannot definitively say that the third party will support that software for the life of the machine. 15-20 years should be the expected life for an automated pipe welding machine and that is a very long time in the software world. Software is rapidly evolving and it can be the case that 15 years down the road your software becomes obsolete from the software company that made it and they will require you to replace that software which is costly and can even require machine hardware upgrades to make it work. Rotoweld employs their own software engineers and every bit of their software is created in-house. We have customers with 15+ year old machines that Rotoweld still supports and updates their software as needed at no charge. Another thing to consider is software subscription fees. If the OEM of the machine does not make their own software you are subject to the subscription fees from the third party provider, which may increase over the years.
In summary, all of these (and a few more) things should be considered when evaluation your options for an automated pipe welding system in today's market. GSI Machinery offers several machines to fit different needs of our customers and we support locally every machine we sell for the life of the machine. Give us a call today to learn more about our welding and cutting automation solutions.
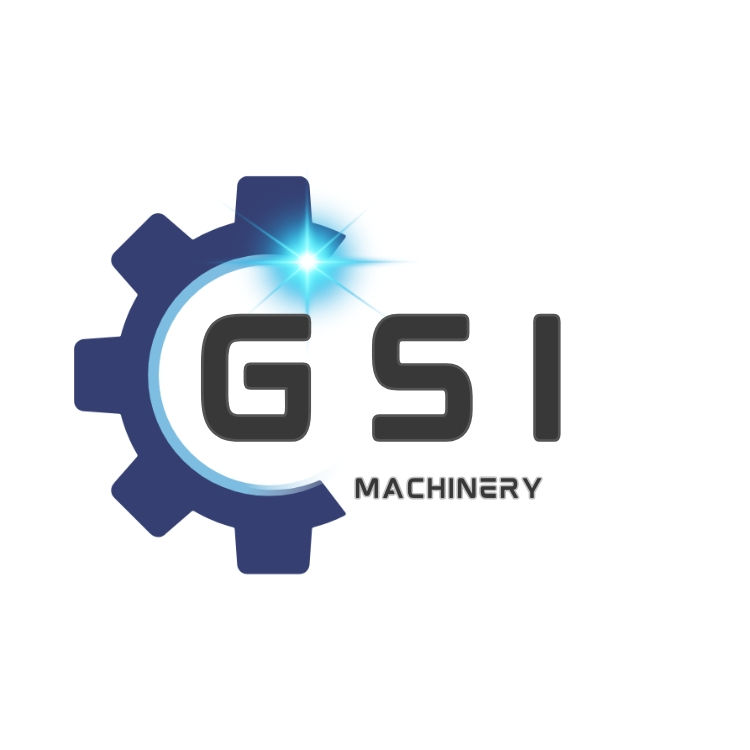