Why 2% Serrated Tungsten is Great for Orbital Welding
- George Ficken
- Feb 19
- 2 min read

In this post we are going to explore what 2% serrated tungsten is and why it is the preferred electrode choice for orbital welding applications. Orbital welding is an automated welding technique in which the electrode "orbits" around the pipe or tube. It is commonly used in industries such as aerospace, semiconductor manufacturing, and pharmaceutical production. When done properly, orbital welding ensures consistent, high-quality welds; great for industries and applications with critical weld joints that must undergo stringent QC requirements. One key component to achieving success with your orbital welding process is the quality and type of your tungsten electrode, which serves as the non-consumable component of the welding arc. Among the various tungsten electrode options, 2% serrated tungsten has gained popularity due to its enhanced arc stability and longevity, making it particularly well-suited for orbital welding applications.
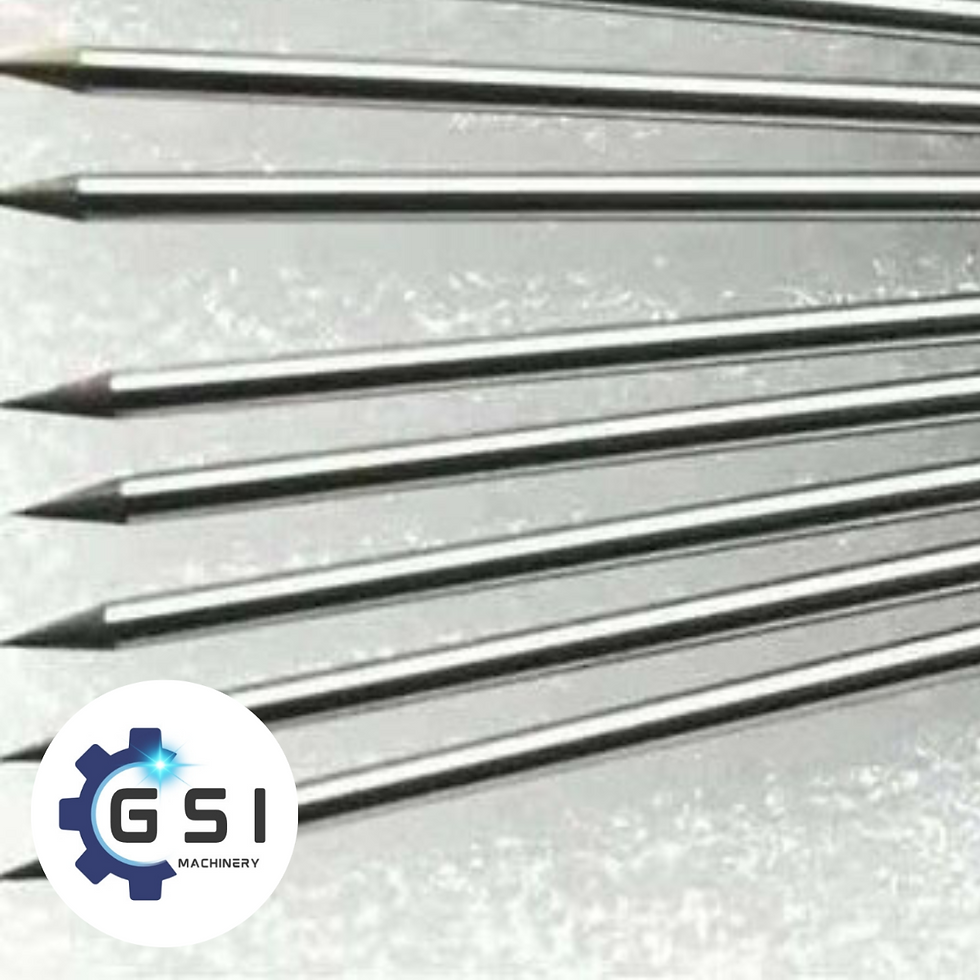
The serrated design of this tungsten electrode features fine grooves along its surface, which improves arc initiation and stability. These serrations help to create a more consistent arc by directing the current flow in a controlled manner, reducing arc wandering and improving penetration. The 2% alloying element, typically thorium or cerium, enhances the electrode’s durability and performance by providing superior conductivity and resistance to wear. This allows for extended electrode life and reduced downtime, which is crucial in high-precision applications where consistency is key.
One of the major advantages of using 2% serrated tungsten in orbital welding is its ability to handle low-amperage DC welding, which is often required for thin-walled stainless steel and exotic alloys. The improved arc characteristics lead to better weld bead formation and reduced defects, such as porosity and tungsten inclusions. Furthermore, the increased control over the arc reduces heat input, minimizing the risk of warping or heat-affected zone (HAZ) issues in delicate components. These benefits make serrated tungsten an ideal choice for applications requiring extreme precision, such as welding in cleanroom environments or assembling aerospace components.
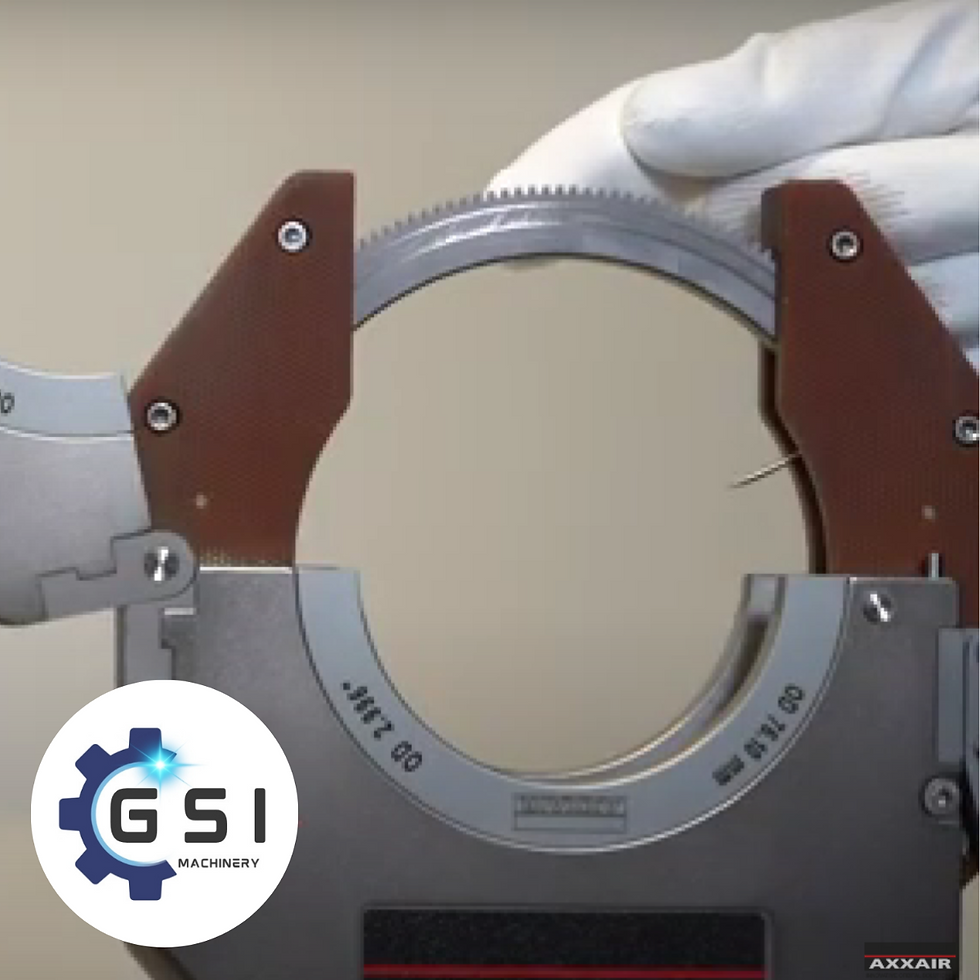
2% serrated tungsten electrodes play a vital role in enhancing the orbital welding process by providing superior arc stability, extended lifespan, and improved weld quality. Their unique design allows for better control of the welding arc, reducing defects and ensuring high-precision results in critical industries. As automation and quality standards continue to rise, the demand for specialized tungsten electrodes like 2% serrated tungsten will only grow, solidifying their place in advanced manufacturing and welding applications.
Reach out to GSI Machinery for expert service, rentals, sales and training 24/7 now offering free training with the purchase of any orbital welding equipment. GSI truly cares about customer success and we want our customers to succeed with the solutions that we provide. We stand behind our equipment 110 percent.